A dredging grab is an essential tool used to dredge material from a water bed or deposit it in a designated location. These devices come in different shapes and sizes to suit a variety of dredging needs, and the manufacture of these products requires a high level of expertise and attention to detail.
Manufacturing a dredging grab involves several complex processes requiring expertise and machinery. The production process begins with the design and engineering phase, where professional engineers work on creating blueprints that meet customer-specific requirements. Once the design is complete, the materials used to make the grab will be selected and prepared for fabrication.
The manufacturing process involves cutting, welding and assembling individual components to create the final product. The cutting process involves cutting steel plates and other materials into the desired shape and size using high-precision machines. Welding and assembling components together requires an experienced and skilled workforce.
The durability and strength of a dredging grapple depends on the quality of the materials used to make it. Manufacturing companies use high-grade steel plates and other materials that can withstand harsh conditions and continuous use. These materials are selected for their ability to resist abrasion, corrosion and impact damage.
The demand for custom dredging grabs has increased significantly in recent years, leading to the development of grab designs that meet specific requirements. Manufacturers are now using advanced software and technology to create complex designs that meet unique customer requirements.
In addition to the manufacturing process, the company also provides maintenance and repair services for dredging grabs. Regular maintenance is essential to ensure the longevity and peak performance of these devices. This service includes inspection and replacement of worn parts, such as teeth and bushings, to maintain the efficiency of the grapple.
Like any manufactured product, dredging grabs undergo rigorous quality control measures to ensure they function optimally and meet the required standards. The quality control process includes testing each grapple to determine its strength and durability. Tensile and impact loads are applied to the grapple using specialized equipment to test its strength and durability.
Manufacturers of dredging grabs must ensure that they meet regulatory requirements and comply with environmental protection standards. The use of environmentally friendly materials and sustainable manufacturing processes are encouraged to minimize the environmental impact of dredging operations.
In conclusion, manufacturing a dredging grab requires a high level of expertise, precision and attention to detail. Manufacturers must use high-grade materials, employ professionals, and utilize advanced technology to ensure the quality and durability of these products. The increasing demand for custom dredging grabs presents an opportunity for manufacturers to create unique designs to meet customer specific requirements while ensuring environmental protection. In a rapidly changing world, the manufacture of high-quality dredging grabs will continue to play an important role in the global dredging industry.
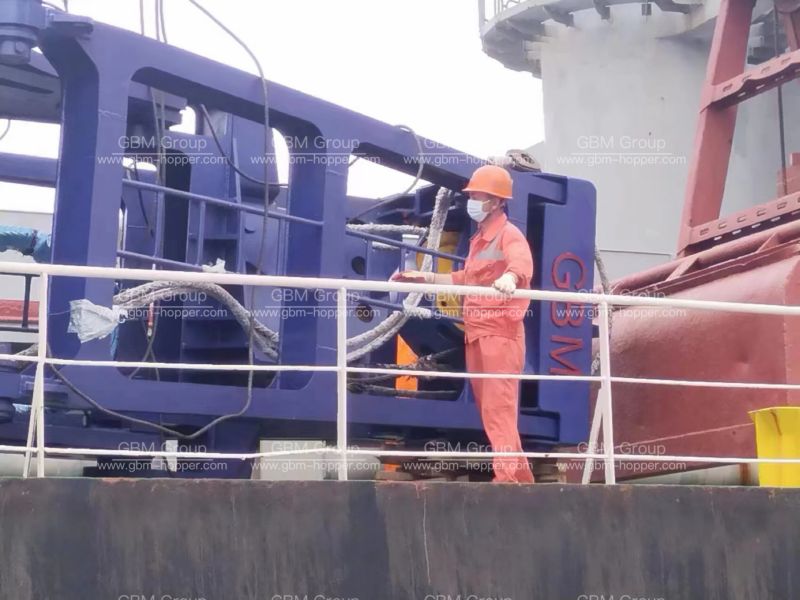
Post time: Jun-13-2023